The AP Precision Approach: Quality Assurance in Metal Fabrication
Metal fabrication plays a crucial role in various manufacturing sectors, serving as the backbone for countless applications within the metal industries. This fabrication process involves transforming raw metal into desired shapes and sizes through a series of processes, including cutting, bending, and welding. Quality assurance is pivotal, as the reputation of a company in metalworking hinges on the accuracy and precision of its work. The AP Precision Approach: Quality Assurance in Metal Fabrication emphasizes these aspects, ensuring that each step in the fabrication processes meets stringent standards. A skilled welding inspector often oversees these operations, ensuring the integrity and functionality of the final products. The combination of advanced techniques and careful oversight leads to exceptional results in metal fabrications, setting a benchmark for quality in the industry.
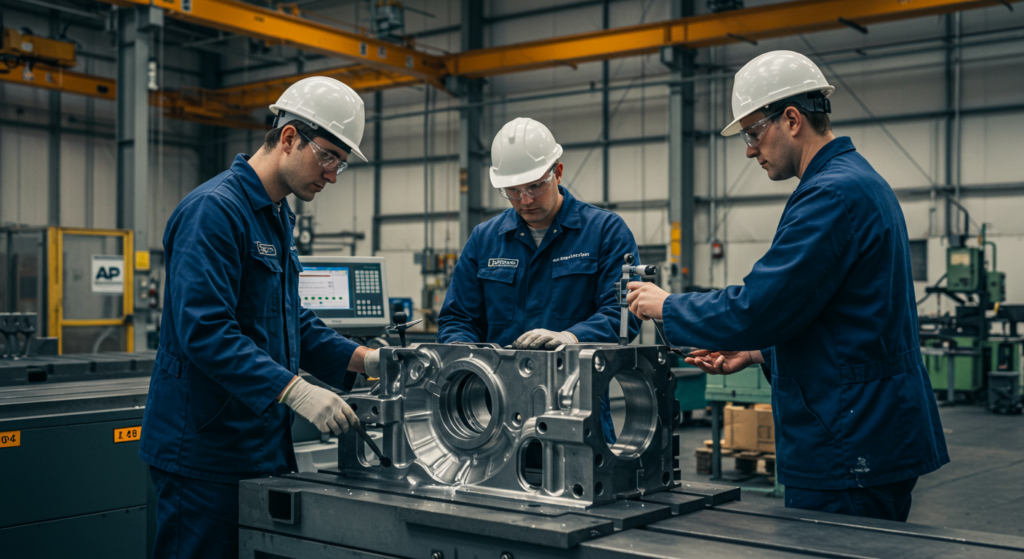
Importance of Quality in Metal Fabrication
Quality assurance plays a pivotal role in metal fabrication, influencing the performance and longevity of fabricated products. Using materials like stainless steel and hot rolled steel requires a deep understanding of their properties. Implementing The AP Precision Approach: Quality Assurance in Metal Fabrication ensures that processes such as CNC machining, spot welding, and additive manufacturing are executed with exceptional accuracy. When working with metal sheets or various metal alloys, maintaining high-quality standards can significantly reduce waste and increase efficiency.
Meeting quality standards is essential for minimizing defects and maximizing product reliability. Techniques employed in metal fabrication, including welding and precision machining, demand rigorous quality control measures. The AP Precision Approach: Quality Assurance in Metal Fabrication emphasizes the importance of accuracy across all stages. This commitment not only enhances the durability of finished products but also builds trust with clients relying on superior craftsmanship in their projects. Each step, from selecting the right materials to executing precise cuts or welds, underscores the significance of quality in this industry.
Key Processes in Metal Fabrication
Metal fabrication consists of various key processes that ensure quality and precision in the final products. Techniques such as laser welding and gas welding play pivotal roles in joining different materials like steel, aluminium, and copper. Machining further enhances the fabrication process by allowing for precise shaping and finishing of components. Adopting The AP Precision Approach: Quality Assurance in Metal Fabrication helps organizations maintain high quality standards throughout these processes, enabling them to meet diverse client needs while ensuring the hardness and durability of the fabricated items.
Material handling equipment is essential in streamlining the movement and processing of raw materials during fabrication. Lean manufacturing principles contribute significantly to the efficiency of the metal fabrication workflow, reducing waste and increasing productivity. By focusing on the integration of processes such as arc welding, machining, and quality assurance, fabricators can improve their overall output and uphold rigorous quality standards. Implementing these processes effectively fosters a culture of excellence in metal fabrication.
The AP Precision Approach: Quality Assurance in Metal Fabrication
The AP Precision Approach: Quality Assurance in Metal Fabrication emphasizes the critical need for stringent quality control processes throughout the fabrication journey. Effective material handling ensures that aluminum alloys and other materials are managed properly, which significantly enhances product quality. By implementing advanced technology in subtractive manufacturing, manufacturers can optimize their processes, leading to heightened reliability. Welder certification, particularly through standards set by the American Welding Society, guarantees that skilled professionals uphold high standards, especially crucial in sectors like the electronics industry where precision is vital. Adopting The AP Precision Approach: Quality Assurance in Metal Fabrication is essential for achieving enduring excellence in production.
- Ensuring thorough inspections at each production stage to identify defects early
- Implementing a robust training program for employees to enhance skills and awareness
- Utilizing state-of-the-art equipment to improve accuracy in fabrication processes
- Conducting regular audits to assess compliance with quality standards
- Establishing clear documentation procedures for tracking quality metrics and improvements
- Fostering a culture of continuous improvement to motivate staff and optimize practices
- Collaborating with suppliers to ensure quality materials and components are used
Core Principles of the AP Precision Approach
The AP Precision Approach: Quality Assurance in Metal Fabrication emphasizes rigorous standards and meticulous attention to detail in every aspect of production. This framework prioritizes the implementation of advanced precision fabrication techniques to ensure products meet the stringent demands of industries like semiconductors. By focusing on high-quality outcomes, the AP Precision Approach equips the metal fabrication industry with the reliability needed to cater to diverse metal fabrication needs, facilitating superior results in precision metal fabrication.
An essential component of the AP Precision Approach is thorough training in various metal fabrication techniques, including tungsten inert gas welding. This method not only enhances the quality and durability of fabricated components but also aligns with the standards set for precision fabrication in precision metal industries. By integrating best practices within their operations, AP Precision Metals sets a benchmark for quality assurance, showcasing how well-executed precision fabrication significantly elevates product performance and customer satisfaction.
Benefits of Implementing the AP Precision Approach
Implementing The AP Precision Approach: Quality Assurance in Metal Fabrication drastically enhances the quality of the end products. This method emphasizes the production of high-quality metal and accurate metal components, ensuring that each part meets strict specifications. Metal fabrication companies utilizing this approach can deliver high-precision sheet metal solutions that cater to various industrial requirements. By focusing on precision fabrication techniques, these companies can tackle complex metal fabrication projects while maintaining consistency and excellence throughout the process.
The benefits are evident in the increased efficiency and reduced waste that comes with The AP Precision Approach: Quality Assurance in Metal Fabrication. Through meticulous attention to the selection of materials and precise fabrication techniques, metal fabrication services can achieve accurate metal parts that lower operational costs. This strategic focus on quality not only boosts customer satisfaction but also establishes a reputation for excellence in the competitive market of metal fabrication solutions. Ultimately, these advantages lead to sustainable growth and long-term success in the industry.
Understanding Metal Fabrication Precision
Precision in metal fabrication is crucial for ensuring that every aspect of a fabrication project meets strict standards and requirements. The AP Precision Approach: Quality Assurance in Metal Fabrication emphasizes the importance of meticulous metal material inspection during the metal fabrication process. High-quality metals, including precision aluminum and high-quality sheet metal, must be selected to achieve optimal results. Various metal fabrication processes, such as sheet metal fabrication, depend on precise fabrication techniques to ensure that the finished products exhibit the necessary durability and accuracy. Employing a robust precision manufacturing process enhances the overall quality and reliability of the fabricated components, catering to diverse fabrication requirements across industries.
Process Type | Description | Common Applications |
---|---|---|
Sheet Metal Fabrication | The process of cutting, bending, and assembling flat sheets of metal. | Automotive parts, enclosures, brackets |
Machining | Removing material from a workpiece to shape it into a desired form. | Precision components, fittings, custom shapes |
Welding | A process of joining two or more pieces of metal using heat and pressure. | Structural frameworks, machinery, piping |
Laser Cutting | Using a laser to cut materials for precision and intricate designs. | Signage, decorative items, industrial components |
Factors Influencing Metal Fabrication Precision
Several factors play a crucial role in determining the precision of metal fabrication. The use of advanced fabrication technologies significantly enhances the accuracy of metal components, ensuring that detailed metal components meet the highest quality standards. Techniques such as precision machining and the utilization of advanced fabrication machinery allow for the production of precision-engineered parts that adhere to stringent specifications. Metal cabinet fabrication, for example, is reliant on these high precision standards to achieve functional and aesthetic goals within the fabrication industry.
The skill level of the workforce is another vital influence on fabrication precision. Experienced operators familiar with various fabrication techniques can utilize metalworking machinery more effectively, resulting in superior outcomes. Implementing The AP Precision Approach: Quality Assurance in Metal Fabrication emphasizes the importance of a well-trained team capable of overseeing production processes. Quality assurance practices contribute to the consistency and accuracy of the finished product, ultimately impacting the overall efficiency of the fabrication process.
Measuring Precision in Metal Fabrication
Precision inspection is critical in ensuring that the fabrication processes meet the stringent industrial manufacturing requirements. At the heart of effective measurement lies the ability to assess the precision accuracy of metal parts produced through various fabrication equipment. High-precision parts are essential for complex applications that demand exceptional reliability. By implementing The AP Precision Approach: Quality Assurance in Metal Fabrication, manufacturers focus on achieving the required dimensional specifications that ensure compatibility and quality throughout the fabrication process.
The high-precision manufacturing landscape requires advanced techniques to accurately measure and inspect fabricated metal materials. Various tools and methodologies exist to gauge the precision of metal forming processes, balancing cost fabrication with the need for quality. Accurate measurements guarantee that each component meets the defined standards, ultimately contributing to the reputation of the manufacturing process. Employing precision inspection protocols allows for the early detection of discrepancies, ensuring that high-quality standards are consistently achieved.
Precision Fabrication Techniques
Advanced fabrication techniques focus on achieving the highest standards of precision in metalworking. The AP Precision Approach: Quality Assurance in Metal Fabrication emphasizes the importance of using high-quality materials and implementing a proper welding procedure to ensure durability and accuracy. CNC precision sheet processes allow for intricate designs and exact specifications, catering to high-precision applications across various industries. Skilled professionals, including society-certified welding inspectors, play a crucial role in maintaining quality throughout the fabrication process. Successful precision sheet fabrication services are key to delivering metal parts that meet stringent quality standards, resulting in superior metal surface finishes and enhanced performance in end products.
Advanced Techniques for Precision Fabrication
Advanced techniques in precision fabrication leverage innovations like CNC sheet metal technologies to enhance productivity. The AP Precision Approach: Quality Assurance in Metal Fabrication emphasizes a lean fabrication approach, allowing for efficient processes that meet diverse manufacturing needs. Precise material preparation is critical in achieving tight tolerances and ensuring the hardness requirement of the final product. By implementing these advanced techniques, manufacturers can produce custom metal structures with improved accuracy and reduced waste.
Achieving high precision measurements is essential in industrial manufacturing. Rigorous quality assurance practices are integral to the overall effectiveness of advanced fabrication methods. Fabrication courses often highlight the importance of mastering these techniques, ensuring that professionals are equipped with the latest knowledge and skills. Employing advanced practices not only elevates the quality of output but also reinforces The AP Precision Approach: Quality Assurance in Metal Fabrication as a standard within the industry.
Comparison of Traditional vs. Precision Fabrication Techniques
Traditional fabrication techniques often rely on manual processes and less sophisticated equipment. These methods can lead to variability in the quality of the fabricated parts and may struggle to meet industry quality standards consistently. In contrast, precision fabrication techniques prioritize high accuracy and employ proven manufacturing systems to address complex manufacturing questions. By utilizing The AP Precision Approach: Quality Assurance in Metal Fabrication, companies can create precision sheet and thin metal layers that are essential for modern industrial manufacturing needs.
The difference in outcomes between traditional and precision fabrication is significant. Traditional methods may not accommodate the same levels of detail and can result in inconsistencies in the finished product. Precision fabrication, on the other hand, ensures compliance with industry-leading quality standards. Quality engineers play a crucial role in the process, overseeing the use of used metals and the production of the next sheet metal to guarantee that each fabricated part meets the required specifications for performance and durability.
Fabrication Technique | Quality Consistency | Equipment Used | Details Handling | Application in Industry |
---|---|---|---|---|
Traditional Fabrication | Variable | Manual Tools | Limited | General Manufacturing |
Precision Fabrication | High | CNC Machines, Laser Cutters | Extensive | Advanced Industrial Manufacturing |
Hybrid Techniques | Moderate | Combination of Traditional and Modern Equipment | Variable | Niche Applications |
A Comprehensive Metal Fabrication Guide
Understanding the essentials of selecting materials for metal fabrication is crucial for achieving high-quality parts and ensuring dimensional accuracy. The AP Precision Approach: Quality Assurance in Metal Fabrication emphasizes the importance of quality control throughout the fabrication process. Utilizing a variety of metals and materials can enhance the performance of custom sheet metal projects. Contemporary manufacturing facilities often implement diverse custom fabrication techniques to meet specific precision sheet requirements. The welding department plays a vital role in producing quality components that align with the standards of modern manufacturing. By prioritizing these elements, manufacturers can achieve superior results in their fabrication endeavors.
Selecting Materials for Metal Fabrication
Selecting the right materials for metal fabrication plays a crucial role in ensuring quality outcomes, particularly when implementing The AP Precision Approach: Quality Assurance in Metal Fabrication. Factors such as the type of metal, thickness, and environmental considerations are essential. High-volume manufacture often requires the use of environmentally-friendly sheet metal, which aligns with modern sustainability practices. Manual welding techniques can be applied to both thick sheet metal and heated metal, ensuring that each joint and seam meets stringent quality standards set by leading sheet metal manufacturers.
Choosing the appropriate materials also influences the overall efficiency of the manufacturing process. The interaction between various metals and the methods used, such as machinery manufacturing and processing manufacturer considerations, is critical. Careful selection minimizes the release of metal vapors during welding, reducing health risks for workers. Each material impacts the next manufacturing step, determining the overall success of the project. Understanding these dynamics is essential for any fabrication specialist aiming to uphold quality assurances like those advocated by The AP Precision Approach: Quality Assurance in Metal Fabrication.
Essential Tools and Equipment in Metal Fabrication
A variety of essential tools and equipment are vital for achieving high-quality results in metal fabrication. Advanced technology plays a crucial role, as seen in the use of welding stations designed for resistance nut welding. These tools allow for uncompromised precision sheet metal custom work, ensuring that the selected metals meet industry standards. The right equipment not only enhances efficiency but also contributes significantly to the overall top-quality production process, which is the core of The AP Precision Approach: Quality Assurance in Metal Fabrication.
The manufacturing side of metal fabrication relies heavily on a robust quality assurance plan that integrates the use of specialized tools. High-quality machinery and instruments are critical for measuring and ensuring precision throughout the production cycle. Employing cutting-edge equipment can optimize the fabrication process, enabling consistent adherence to quality benchmarks while delivering superior products. This commitment to excellence exemplifies The AP Precision Approach: Quality Assurance in Metal Fabrication, where precision, quality, and reliability are paramount.
Precision Fabrication Applications
Precision fabrication finds extensive applications across various industries, driven by the need for quality parts that meet rigorous design specifications. By employing The AP Precision Approach: Quality Assurance in Metal Fabrication, manufacturers can ensure high-quality products that adhere to precise design requirements. This methodology is particularly valuable in pipe fabrication, where accurate components are crucial for functionality and safety. The integration of quick response manufacturing alongside subtractive manufacturing methods enhances efficiency and responsiveness to changing demands. Supporting processes such as powder coating service also play a vital role in achieving the desired finish for stainless steel products. With access to diverse manufacturing resources, businesses can optimize their operations and deliver exceptional results.
- Precision fabrication is essential in aerospace for producing lightweight and durable components.
- The automotive industry utilizes precision fabrication for creating intricate parts that enhance vehicle performance.
- Medical devices rely on precision fabrication to ensure safety and compliance with strict health regulations.
- Electronics manufacturing incorporates precision fabrication for intricate circuit boards and components.
- Construction projects benefit from precision fabricated elements that ensure structural integrity and longevity.
- Precision fabrication supports the development of consumer goods with high aesthetic and functional standards.
- The energy sector uses precision fabrication for components in renewable energy systems, ensuring efficiency and reliability.
Conclusion
The importance of quality assurance in metal fabrication cannot be overstated. The AP Precision Approach: Quality Assurance in Metal Fabrication emphasizes the need for accurate designs and the use of advanced machining centers. Various welding processes play a crucial role in ensuring that the assembly of components meets the desired specifications. Choosing suitable materials, including high-performance alloys, enhances product reliability and ensures accurate parts are produced consistently. Emphasizing methods compliant with American welding standards ensures that the end products not only meet client expectations but also stand the test of time in their respective applications. This dedication to precision ultimately defines the success and reputation of any fabricator in the industry.
FAQS
How do AP Precision Metals ensure high-quality metal components through their precision fabrication techniques?
AP Precision Metals utilizes advanced CNC precision technology in their quality control/quality assurance processes. Their precision fabrication enhances the production of high-quality metal components, ensuring that all utilized metals and materials meet stringent ISO ensures precision standards. By incorporating multiple welding processes, AP Precision Metals guarantees that their manufacturing processes adhere to the highest quality standards as documented in industry resources such as the Welding Journal.
What are the specific steps that AP Precision Metals take to ensure that the metals/materials used in their production meet the standards for high quality metal components?
AP Precision Metals employ a rigorous quality assurance approach that includes multiple related manufacturing processes. Their precision fabrication entail extensive testing and inspection of materials to ensure that they utilize metals that meet stringent quality standards. This process helps them achieve high quality metal components that are reliable and durable.
What practices does AP Precision Metals implement to maintain quality assurance in their metal fabrication process?
AP Precision Metals employs rigorous quality assurance practices throughout their metal fabrication process to ensure that all metals/materials meet industry standards and client specifications. This includes regular inspections, testing of metals/materials, and adherence to precise fabrication techniques.
What certifications and industry standards does AP Precision Metals adhere to in their pursuit of high-quality metal fabrication?
AP Precision Metals adheres to various certifications and industry standards to ensure high-quality metal fabrication, including ISO 9001 for quality management systems and compliance with ASTM standards. These standards ensure that the metal components produced meet rigorous quality assurance requirements, promoting reliability and performance in their end products.
What innovative technologies does AP Precision Metals utilize to enhance their quality assurance in metal fabrication?
AP Precision Metals employs innovative technologies such as laser cutting, CNC machining, and precision welding to enhance their quality assurance in metal fabrication. These technologies allow for greater accuracy and consistency in producing high-quality metal components, ensuring that every piece meets rigorous industry standards.